Recent Posts
-
Easy-to-Use Door Drilling Clip – Step-by-Step Guide for Precision Holes | PCS Hardware
Achieve perfect door drilling effortlessly with our Door Drilling Clip! Follow simple steps: drill center hole, insert fixer, and drill side holes. Even beginners get professional results. Contact us for durable, high-precision hardware solutions!
-
High-Quality Door Drilling Clip – Durable Steel, Dual Versions, Free-Choice Direction | PCS Hardware
Boost efficiency with our durable Door Drilling Clip, made from high-quality steel for long-lasting use. Choose between simple or clamp versions for precise positioning. Drill in any direction (north-south or east-west). Contact us today!
-
Economy Door Handles: Balancing Cost & Quality with EN1906 Standards | PCS Solutions
Discover how PCS economy lever handles deliver reliable performance while meeting EN1906 standards. Learn to identify quality differences in budget-friendly hardware. Contact us for risk-managed procurement solutions.
-
Economy Door Hardware: Strategic Value & Risk Management Solutions | PCS
Discover how economy-range door hardware creates market access while managing risks. Our solutions include EN 1906 Grade 2 certification & strict quality control for reliable, competitive products. Contact us for strategic partnerships!
-
Ultra-Slim Magnetic Door Hardware: 2.9mm TH104M Latch & 90s Tool-Free Installation | ANSI/BHMA Certified
World's thinnest 2.9mm magnetic door handles with color-matched flush mounting. Features ±0.2mm alignment tech enabling 90-second installation. 3mm concealed rose plate meets ADA compliance.
-
Door Stopper Fastener Loosening
Solve cyclic loading failures with Grade 8.8 bolts, nylon locknuts & ISO 10964 adhesives. Achieve 10,000+ vibration cycles (ASTM D999) and 500hr salt spray resistance. 400% lifespan extension proven.
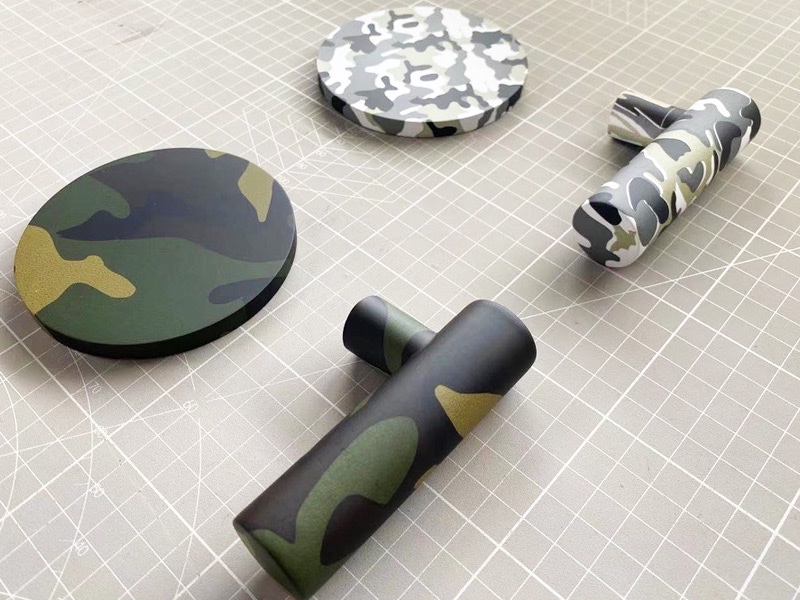
Analysis of Hydrographic Printing Application in Door Hardware Surface Finishing
I. Process Advantages
1. Exceptional Process Adaptability
Complete pattern coverage on complex geometries
Customizable designs with client-driven pattern creation
2. Cost Efficiency
Industry-leading affordability for customized finishes
80%+ mold cost reduction for new product development
3. Family-Style Design Extension
Unified aesthetics across product lines (handles, locks, door closers, etc.)
Seamless pattern transitions enhance brand consistency
4. Environmental Durability
Derived from motorcycle exhaust treatment technology
Withstands -20°C to 80°C; 40% improvement in UV resistance (ASTM D4587 compliant)
II. Process Limitations
1. Minimum Order Requirements
Base production threshold: 2,000 standard units per order
5,000-unit minimum for specialized designs (e.g., lever handles)
2. Cost Structure Considerations
15-20% higher unit cost vs. standard finishes
Marginal cost reduces to 92% of conventional processes for 10k+ unit orders
3. Production Timeline Constraints
72-hour curing cycle for pattern stabilization
Multi-color printing increases lead time by 15%