Recent Posts
-
Easy-to-Use Door Drilling Clip – Step-by-Step Guide for Precision Holes | PCS Hardware
Achieve perfect door drilling effortlessly with our Door Drilling Clip! Follow simple steps: drill center hole, insert fixer, and drill side holes. Even beginners get professional results. Contact us for durable, high-precision hardware solutions!
-
High-Quality Door Drilling Clip – Durable Steel, Dual Versions, Free-Choice Direction | PCS Hardware
Boost efficiency with our durable Door Drilling Clip, made from high-quality steel for long-lasting use. Choose between simple or clamp versions for precise positioning. Drill in any direction (north-south or east-west). Contact us today!
-
Economy Door Handles: Balancing Cost & Quality with EN1906 Standards | PCS Solutions
Discover how PCS economy lever handles deliver reliable performance while meeting EN1906 standards. Learn to identify quality differences in budget-friendly hardware. Contact us for risk-managed procurement solutions.
-
Economy Door Hardware: Strategic Value & Risk Management Solutions | PCS
Discover how economy-range door hardware creates market access while managing risks. Our solutions include EN 1906 Grade 2 certification & strict quality control for reliable, competitive products. Contact us for strategic partnerships!
-
Ultra-Slim Magnetic Door Hardware: 2.9mm TH104M Latch & 90s Tool-Free Installation | ANSI/BHMA Certified
World's thinnest 2.9mm magnetic door handles with color-matched flush mounting. Features ±0.2mm alignment tech enabling 90-second installation. 3mm concealed rose plate meets ADA compliance.
-
Door Stopper Fastener Loosening
Solve cyclic loading failures with Grade 8.8 bolts, nylon locknuts & ISO 10964 adhesives. Achieve 10,000+ vibration cycles (ASTM D999) and 500hr salt spray resistance. 400% lifespan extension proven.
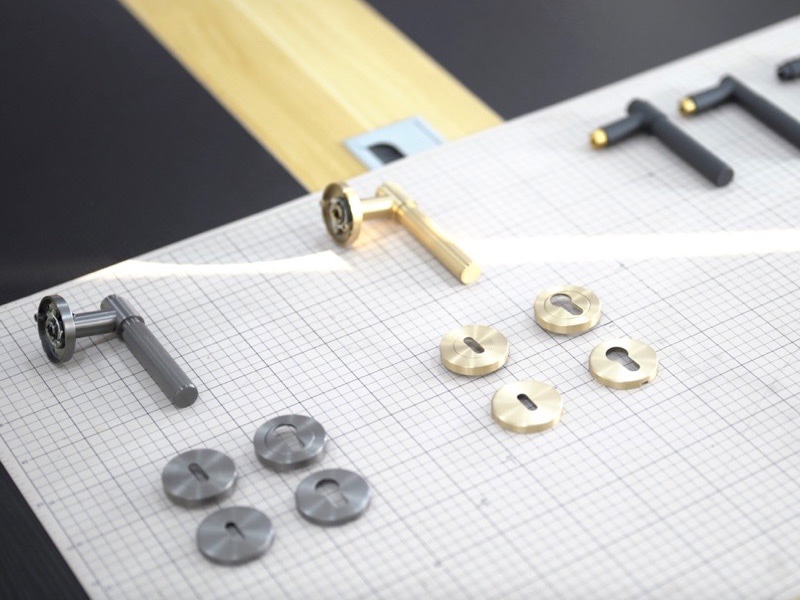
Immersion Plating Process Analysis
Advantages
1, Color Versatility:
Supports 50+ metallic finishes (e.g., champagne gold, brushed nickel)
2, Cost Efficiency:
40-60% lower initial cost compared to PVD coating
Critical Process Challenges
1, Hollow Component Risks:
Requires precision drying protocol:
Standard components: 30min @ 80°C (ISO 2812-3)
Complex geometries: 90-120min with rotational drying
2, Latent Defect Mechanism:
Residual plating chemicals (pH 2.5-3.5 solutions) accelerate:
Subsurface corrosion (ASTM G85 Annex A3)
Electrochemical migration (IPC-610H Class 3)
3, Quality Control Limitations:
Visual inspection misses 38% of internal residues (per NACE SP0492)
Market Preference Trends
Product Type | Preferred Finish | Key Drivers |
Hollow Components | Glossy Immersion | Cost-effectiveness |
Solid Components | Matte Electro/PVD | "- 35% higher corrosion resistance - HV300-500 surface hardness" |
Technical Advisory
1, For Architectural Projects:
Specify PVD coating (EN 1670 Grade 4) for coastal environments
2,Budget-Conscious Applications:
Use immersion plating with extended 72hr salt spray certification
3, Luxury Residential:
Combine matte electroplating with nano-sealing technology
Quality Assurance Protocol
Implement XRF thickness mapping for hollow components
Conduct electrochemical impedance spectroscopy (EIS) quarterly
Maintain plating solution analysis per ASTM E1473